Inventory management is critical for construction projects and can make or break your success. With so many moving parts, managing materials efficiently isn’t just a nice-to-have; it’s essential. Even small slip-ups in tracking or ordering can cause big headaches. Mastering inventory management not only saves you time and money but also boosts your project’s productivity and client satisfaction.
What’s in this article?
- 4 Common Inventory challenges
- 5 Ways to improve inventory accuracy in construction projects
- 4 Must-haves to manage inventory
- Final solutions to take action
- FREE Construction Inventory Management Self-Assessment – Rate your company strategy!
Common Inventory Challenges in Construction Projects
Every construction company faces inventory management challenges, but some issues pop up more frequently:
1. Inaccurate Inventory Tracking
Are you still juggling spreadsheets or sticky notes? Manual tracking often leads to errors, misplaced materials, or overlooked stock, which hurts your inventory accuracy. Improving inventory accuracy in construction projects starts with ditching outdated methods.
2. Material Shortages and Overstocking
Running out of materials mid-project causes costly delays, while overstocking ties up cash and creates storage headaches. Both scenarios can be avoided with better forecasting and inventory controls.
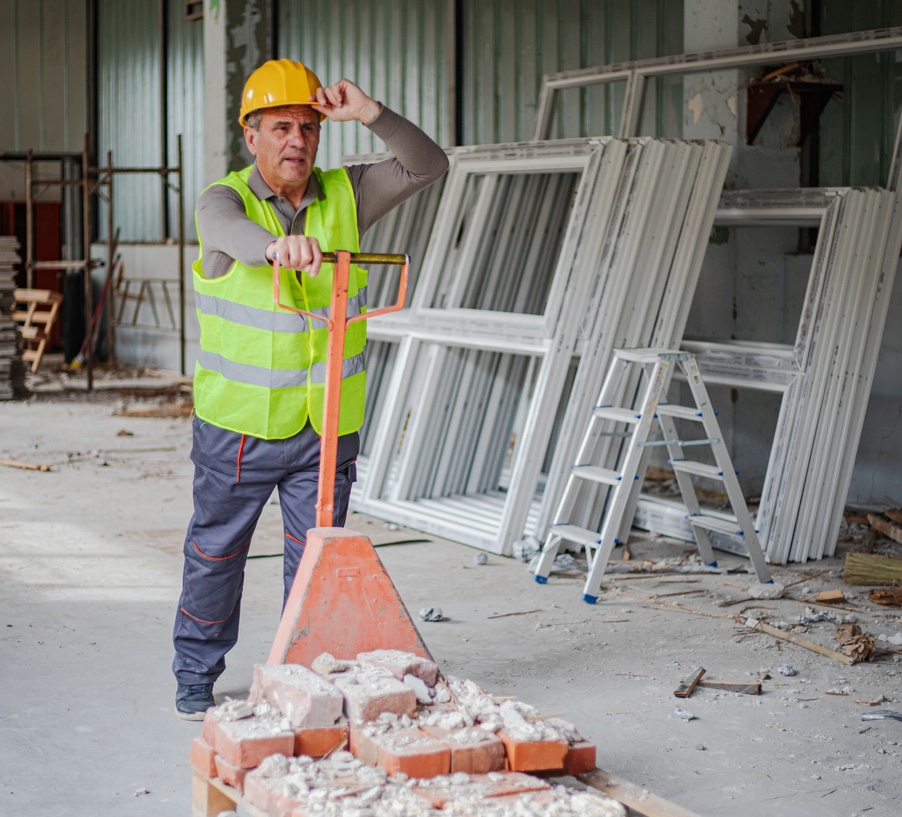
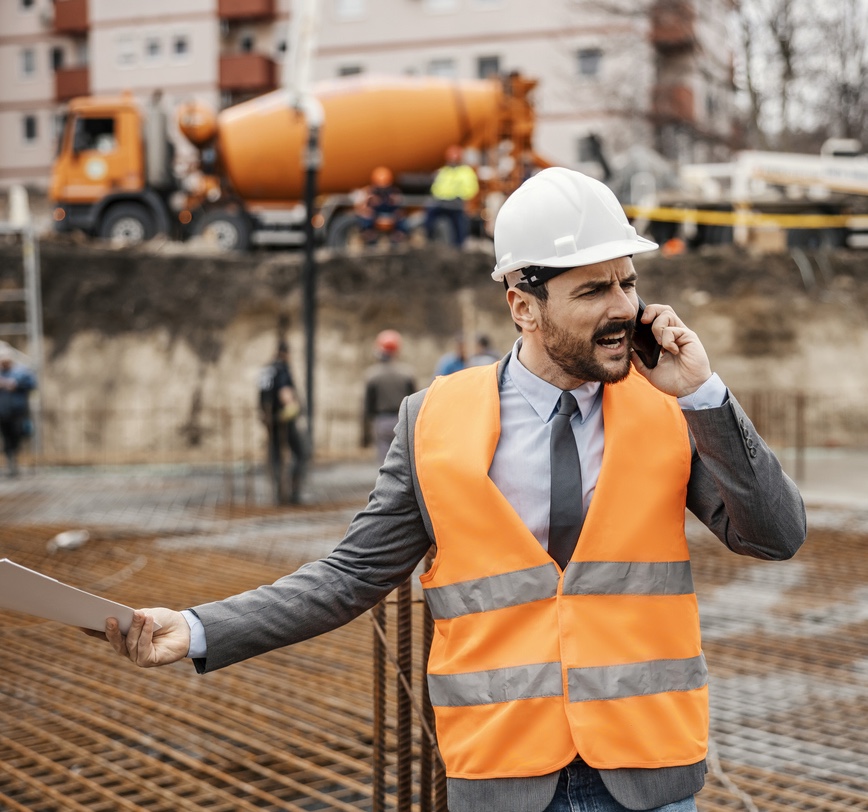
3. Poor Communication and Coordination
Lack of communication between sites or teams leads to duplicated orders or missed updates. Efficient inventory management for construction projects depends on a centralized system that everyone trusts.
4. Storage Inefficiencies and Theft
Disorganized storage slows down crews, and theft or loss of materials adds unexpected costs. There are over 11,000 incidents of equipment theft each year in the U.S., with a very small recovery rate of less than 7%. Optimizing storage and improving site security are key steps toward minimizing waste.
How to Improve Inventory Accuracy in Construction Projects
Improving inventory accuracy is foundational to better project outcomes. Here’s how you can tackle it:
- Adopt the best materials tracking software for construction companies that offers real-time updates and mobile accessibility.
- Use barcode scanning or RFID technology to reduce manual errors.
- Train your staff on consistent inventory practices and software usage.
- Regularly audit inventory to catch discrepancies early.
- Use smart software that can schedule and track expensive equipment.
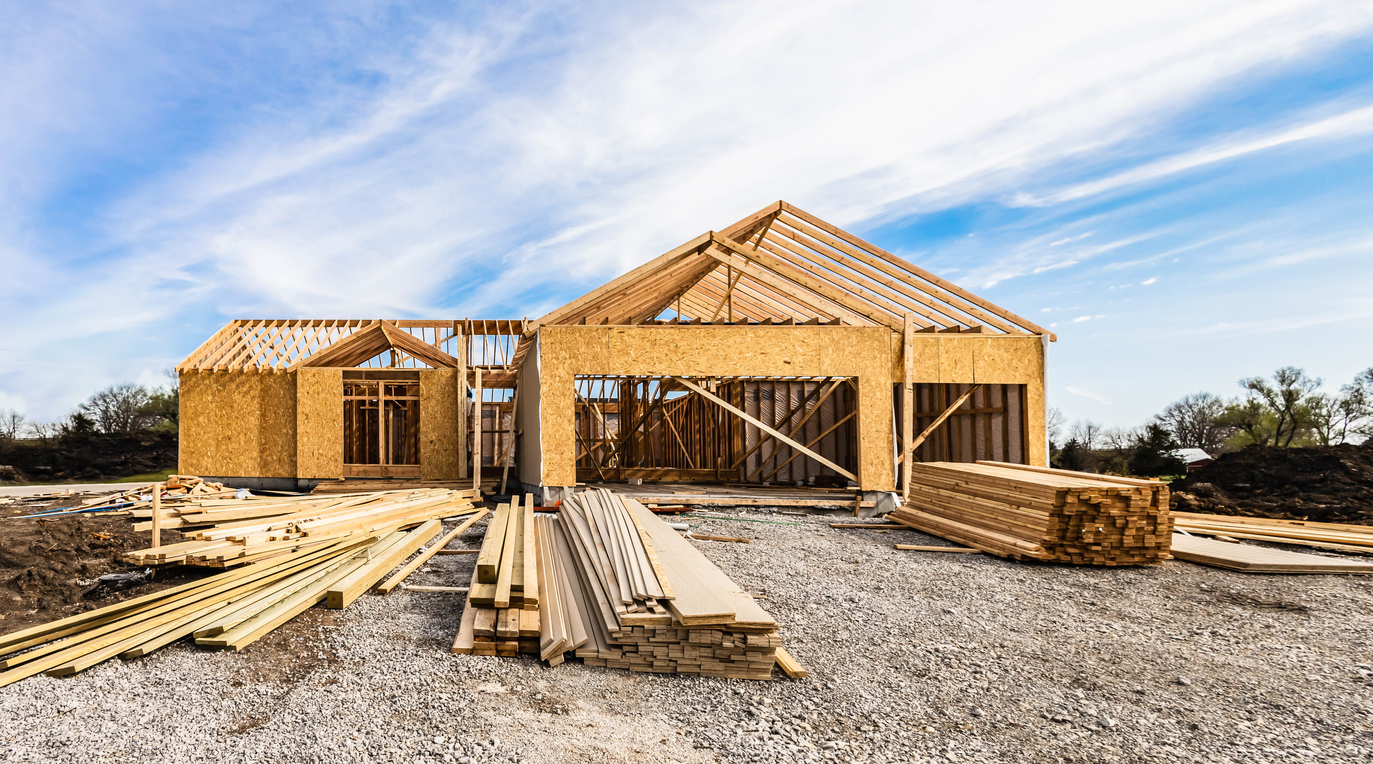
Managing Inventory for Field Service Businesses and Construction Projects
Whether your company focuses solely on construction or also offers field services, inventory management practices overlap. Managing inventory for field service businesses requires:
- Mobile-friendly inventory systems for on-the-go tracking.
- Integration between field operations and central offices.
- Automated alerts for low stock and reorder points.
- Accurate data syncing across multiple locations.
By leveraging tools designed for these challenges, your business can reduce downtime and increase responsiveness on every project.
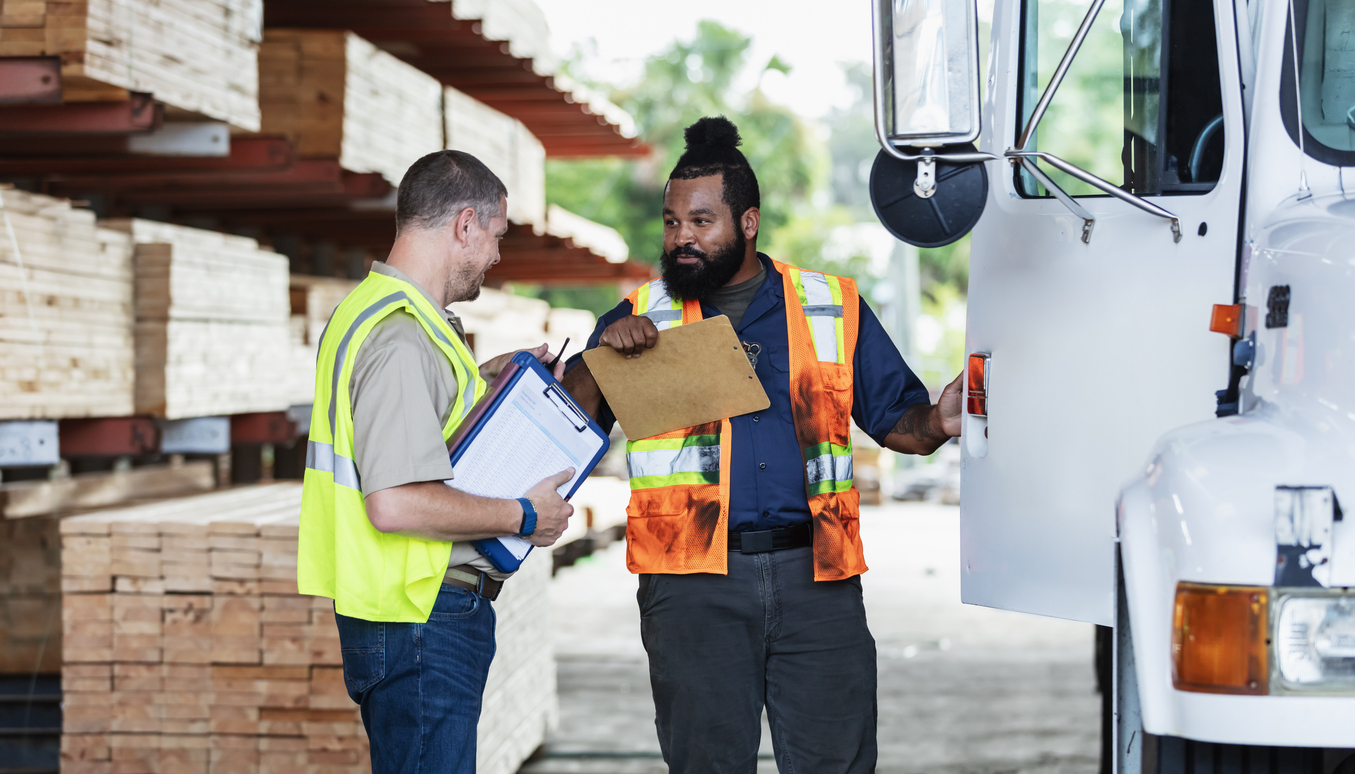
Solutions to Your Inventory Challenges
Fixing inventory issues doesn’t have to be complicated. Here are practical solutions to elevate your inventory management:
1. Invest in Robust Inventory Management Software
This is crucial. Whether you go with our software or choose something else, Modern software solutions like B3 Software provide the tools to automate tracking, forecast needs, and maintain accurate records across projects.
2. Centralized Inventory Data
Keeping all inventory information in one accessible place improves communication and decision-making.
3. Train Your Team
Well-trained staff to make the most of your systems and follow best practices consistently.
4. Implement Forecasting and Analytics
Use past data and predictive analytics to plan your material needs effectively and avoid costly shortages or excesses. Bonus points if all that data is automated in real-time (That’s how we do it here at B3!) Check out our article, Solutions for Managing Construction Inefficiencies to learn more.
5. Enhance Storage Organization and Security
Well-labeled, secure storage areas reduce loss and speed up material retrieval.
The Bottom Line
In the competitive world of construction, inventory management for construction projects is a vital strategy to stay on time and on budget. By focusing on improving inventory accuracy, adopting the best materials tracking software for construction companies, and applying proven management techniques, you’ll reduce costly mistakes and maximize productivity.
Ready to implement a custom construction software in your business? We would love to be a part of your success journey. Request a free demo to see how we can help you meet your goals.
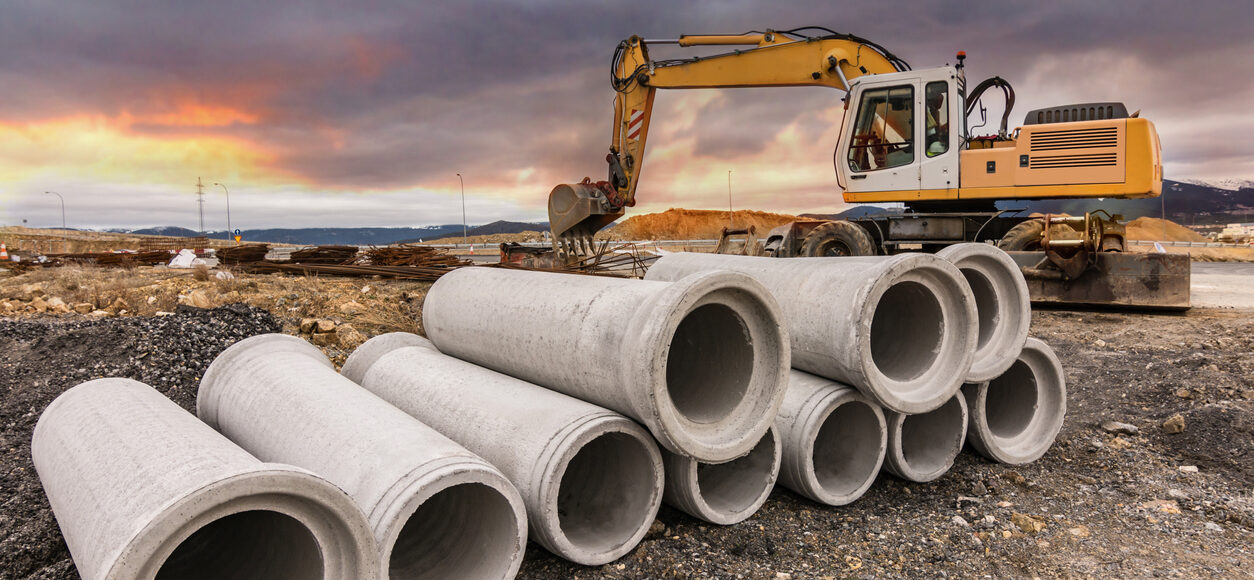